ATLAS ITk
Production of pixel modules and quality control of flexible PCBs
We are currently assembling and testing around 200 production modules, equipped with the front-end chip version RD53C (ITkPixV2) based on the developments made by the RD53 Collaboration, for the Outer Barrel region of the ATLAS ITk (Fig. 1).
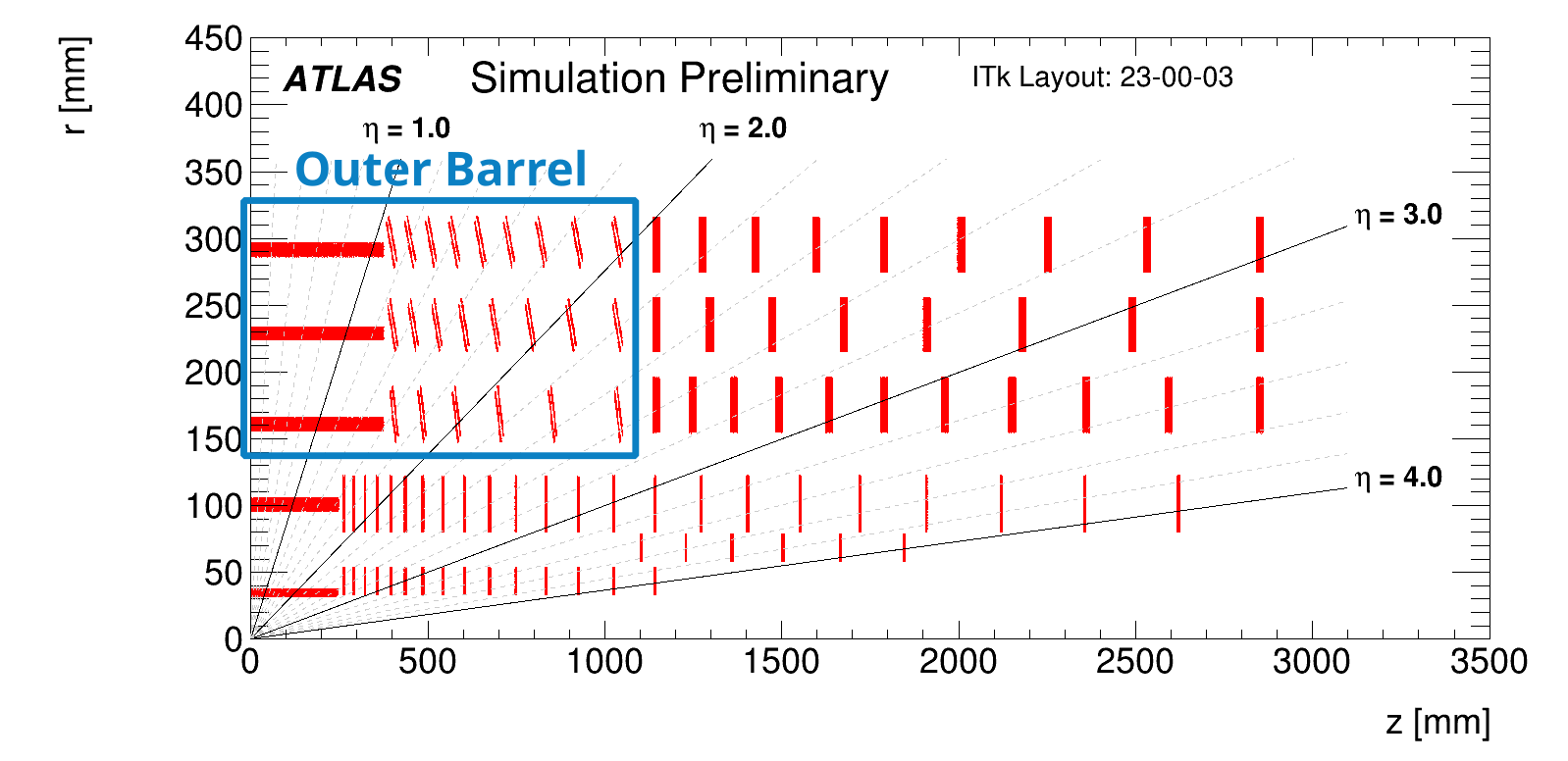
In preparation for the module production phase, our group designed and built a dedicated setup for testing modules electrically (Fig. 2) and simulating thermal stress of the modules, and a dedicated cleanroom was set up to assemble modules in a dust-free environment. The production of pixel modules was successfully trained using silicon dummy, prototype and preproduction modules. It is important to reach highest precision during the assembly (Fig. 3) and to ensure that the modules are of best quality regarding their dimensions and electrical and thermal properties after each assembly step.
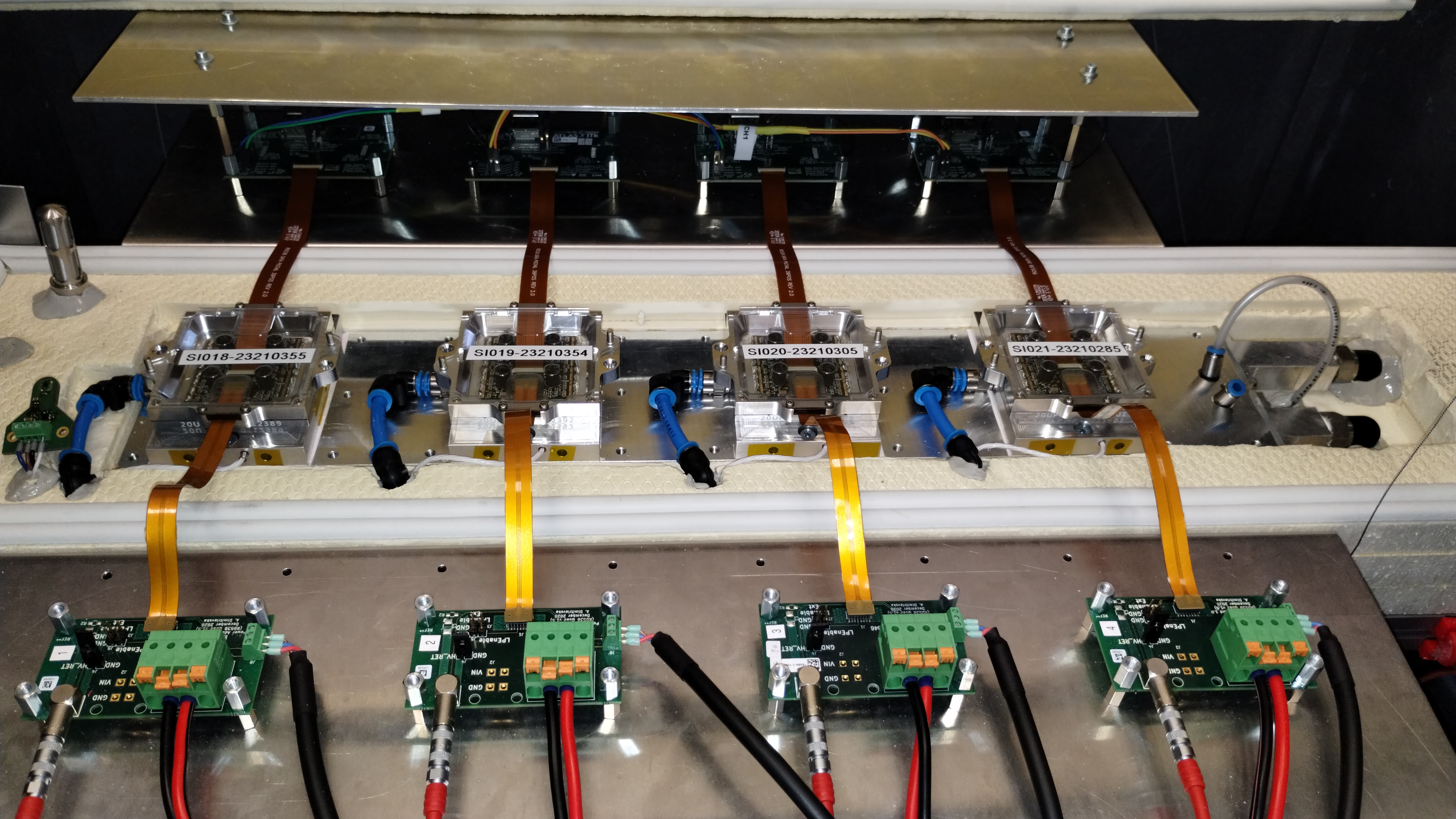
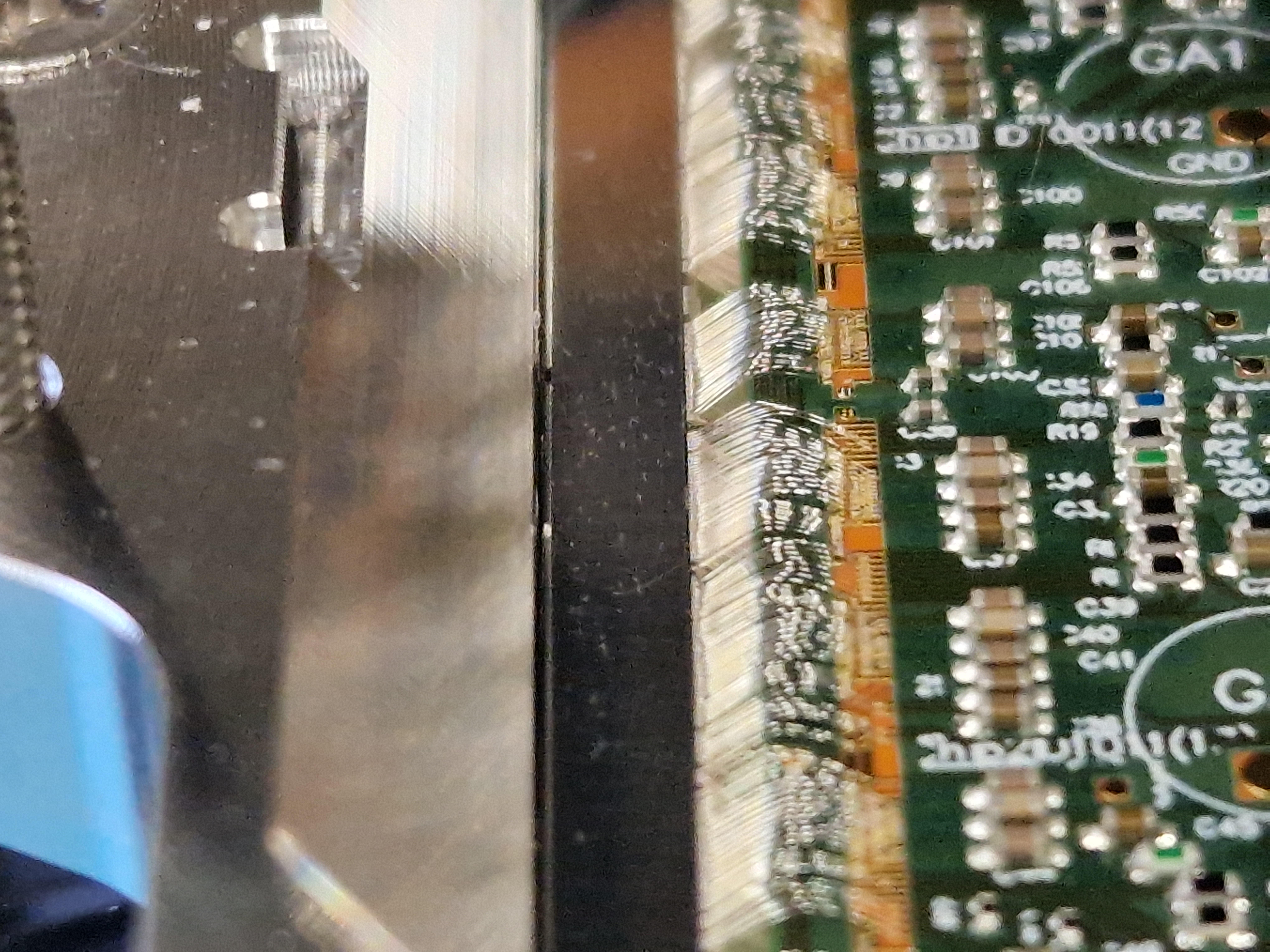
In addition to module assembly and testing, Siegen also performs the quality control of all 2000 flexible PCBs (flexes) needed for the German Outer Barrel pixel module cluster. The members of this cluster are Bonn, Göttingen and Siegen. During this quality control, we control if the flexes produced in industry fulfill stringent requirements on the electrical performance and on the dimensions required for building good production modules.